每次登机,在乘务员笑脸相迎之后,最先映入你眼帘的是什么?想必是客舱内排列整齐的飞机座椅了。这些看似熟悉的飞机座椅,其设计、开发、检测和生产却是一个精密复杂的过程,有非常高的技术标准和要求。今天,我们就来聊聊飞机座椅那些鲜为人知的故事,保准让你大开眼界!
航空领域的“高级定制”
飞机座椅这一与每位旅客接触最为密切的机上设备,却并非“千篇一律”的标准化。因为每家航空公司都会对自己所经营航线的座椅提出特定的功能需求,比如颜色、小桌板、触摸屏、阅读灯和许多其他细节。甚至还有外国航空公司提出,需要一个能方便旅客将宠物狗拴在座椅上的解决办法……可以说,每一种飞机座椅背后都是一项庞大的工程,从招标、设计、报价、技术规格,到与供应商、供应链相关的项目开发阶段,这之后还有产品的工业化和适航取证等环节。
这一切都是为了让航空公司拥有一个符合其品牌形象的座椅产品,从众多竞争对手中脱颖而出。以公务舱座椅为例,一个项目从构思到开展,要耗时12个月~20个月不等。往往一个颜色上的变动,就意味着要重启另一个项目。不仅如此,座椅的外观还要符合每个国家或地区的文化与审美,比如北欧的暖色调、亚洲国家的柔和色彩,以及中东国家的浮华绚丽……所以,座椅生产厂商很难持有一个绝对适用于所有航空公司的“产品目录”,每一种飞机座椅的开发都是航空领域的“高级定制”。
一个飞机座椅在成功出产之前需要满足多项指标,其中一项便是坚固。飞机座椅必须经久耐用,因为其每天24小时里约有18小时都在被使用。按照如此强度,一个飞机座椅只需要经历一个月的时间,便耗尽了一个汽车座椅的寿命。一个飞机座椅必须能够与其所装配的飞机一道,经历数千次“着陆和起飞”循环。每个飞机座椅在“退役”前,平均服务过350万名旅客。
据了解,飞机座椅市场的估值弹性非常大,其年产值预估在41亿美元(约合人民币275亿元)~160亿美元(约合人民币1074亿元)。最新的报告显示,空客大约有7000架飞机订单,波音有5000架。以空客A321neo的200个经济舱座椅为例,其单机座椅成本约在4000美元到80000美元不等。这是一个不小的市场规模,尤其是商务舱和头等舱的座椅,其成本能达到6位数。因此飞机座椅制造商需要完成数量庞大的客机座椅生产任务。
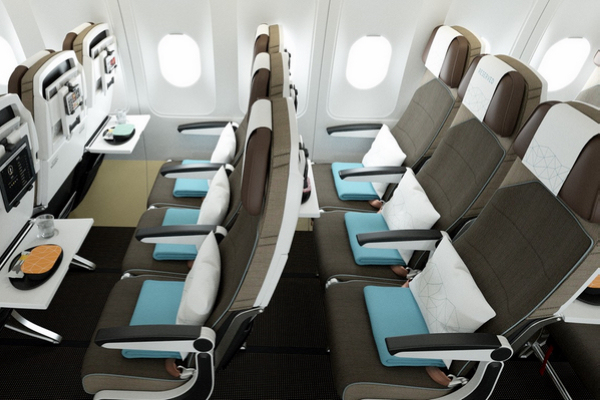
阿提哈德航空全新经济舱座椅
高空中的“寸土寸金”
飞机座椅的设计与生产是一个极其复杂、精细、充满技术挑战的过程。譬如,一个经济舱座椅就包含1000多个零部件,公务舱座椅的零件数量更要翻倍。所以座椅制造商需要把每个零部件的重量都考虑在内,这是拥有竞争力的关键,因为积少成多后,一个经济舱座椅的重量就可达到8公斤~13公斤。再比如,客户可能会根据其餐盘指标、用餐时施加其上的压力,对座椅上的小桌板的长度提出要求;侧扶手也是如此,因为要考虑到旅客可能会坐到扶手上,要顶得住高达180公斤的压力……如此多的指标被转化为数学计算并进行3D建模,这是生产制造的前提基础。以赛峰航空座椅公司为例,其设计中心内就有100多位专员围绕座椅骨架、相关设备、装配、电气集成、外饰面和硬件等领域工作。他们通过不断的努力,持续改善旅客座椅舒适度和人体工学设计,通过个性化产品为航空公司客户提供差异化服务的可能性,优化可利用的客舱空间。
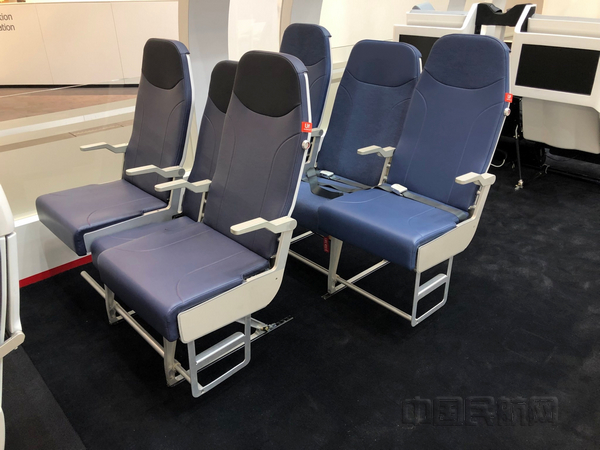
美国联邦航空局(FAA)Molon Labe公司设计的S1型中间座椅
商务舱座椅的设计更为复杂,可以直接体现出座椅制造商的技术水平和实力。根据要求,机上50%的座位必须做到方便行动不便的旅客进出。在经济舱座椅上只需抬起侧扶手即可解决的问题,换到商务舱座椅上则需要投入数百小时的工作。在有限的空间里,既要把服务于旅客的所有功能都囊括其中,又要让人觉得有活动空间。从在电脑上设计到最终生产成品,生产一种商务舱座椅需要2年~3年的时间。这背后是无数个设计方案的反复推敲和各种创新技术的应用尝试。
从占地面积上看,2个商务舱座椅所占面积相当于3排~4排经济舱座椅。如果把旅客乘坐飞机比作租用机上面积,那座椅所占的每块面积都是寸土寸金的。以机组人员座椅为例,由于机组人员与普通旅客不同,无须买票旅行,不为航空公司带来票务收入,所以他们所使用的技术座椅更需要尽可能优化空间。这就是为什么每个此类座椅都被赋予更多功能。以TOS观察员座椅为例,其可被收放在驾驶舱的隔板之后,以节省空间。ATR座椅的设计更是巧妙,其位于过道尽头,在不使用时,可充当隔开驾驶舱和飞机其他部分之间的一道门;当遇到紧急状况时,座椅可以被拆解下来当作担架。一种优秀的飞机座椅一定要尽可能少地占用空间,所以座椅制造商们一直努力在不断优化产品的功能和空间的使用。
拥有“身份证”的严格测试
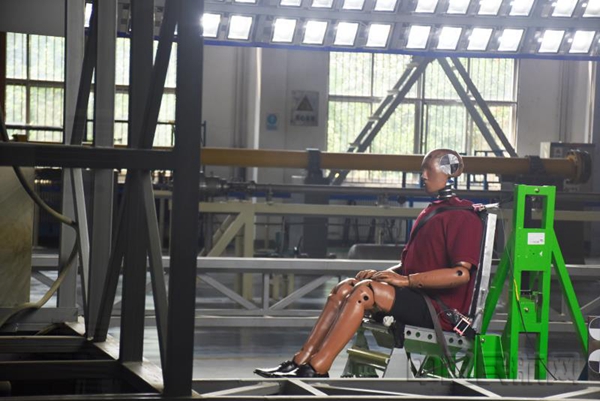
GA20飞机安全带及座椅动态冲击试验
在全球范围内,大约有25家飞机座椅制造商,创新和价值是他们的核心竞争力。其中4家主要的座椅生产商是柯林斯航空航天公司、瑞卡罗公司、赛峰公司和汤普森航空座椅公司。每一部座椅的生产都可以追根溯源到操作员工,而且都会经过严格的测试后再投入使用,
在赛峰航空座椅公司位于法国的生产线上,根据装配需求,共配备5个~10个岗位。一种座椅从上产线到成型,大致需要20分钟~35分钟,以经济舱座椅为例,大概需要20多分钟;随之而来的是最终检查,由一位员工操作,这可谓给座椅产品颁发“身份证”,在这个环节一旦发现任何问题,有关信息必须在48小时内被反馈。
以撞击测试为例,座椅严苛的标准从中可见一斑。该测试往往需要持续数月甚至数年的时间。任何偏差都是不被允许的,因为每项测试都需要3个~4个操作员一整天的准备,不能留有任何犯错的余地。在测试空间内,一个座椅被安装在一个模仿飞机墙壁的蓝色金属结构上,座位上坐着一个人体模型。除了测量腰椎压力的力传感器,模型的头部、胸部和骨盆都安装了加速度计,代表客舱内壁的蓝色框架用于测量内壁的偏转、变形。在这一过程中,能获取的数据越多越好,因为几秒钟的测试就需要大量准备工作,且耗资昂贵。人体模型、座椅、金属框架……这一切都被植入了收集冲击数据的传感器,用以分析冲击,尤其是座椅衰减冲击的能力。座椅会被弹射器以45公里/小时抛出数十米。
每次动态测试都对应一个场景,以机组人员的座椅测试为例,需要根据不同的场景进行24次动态测试。在放置弹射器的轨道末端,竖着许多金属棒,其姿态像是古代战场上士兵冲锋时架起的长矛,这实际上是用于吸收冲击的减速系统:弹射器发射,在短短几秒内,以雷鸣般巨响撞击到减速装置上。装在测试区四周的几台摄像机将整个过程拍摄下来。影片随后将以每秒1000张图像进行剪辑,结合传感器收集到的数据,用于测试后的分析并找出可以改进的地方。(中国民航网 通讯员崔广琪)